The commercial dishwasher industry has evolved significantly to meet diverse operational requirements across foodservice, healthcare, and hospitality sectors. This analysis examines three distinct customization tiers that manufacturers offer to address varying market demands, from basic parameter adjustments to complete original equipment manufacturing solutions.
Executive Summary
The commercial dishwasher market demonstrates robust growth with varying projections from industry analysts, reflecting the increasing demand for customized solutions across different applications. Our analysis identifies three primary customization tiers: Parameter Selection, Module Modification, and OEM/ODM development, each serving distinct market segments with specific cost structures and implementation timelines.
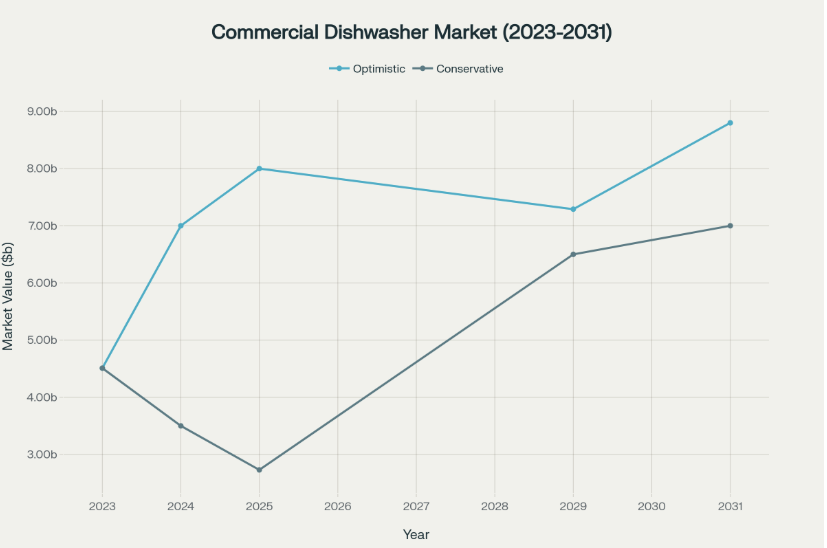
Market growth projections for commercial dishwashers showing varying estimates from different research sources
The market growth trajectory indicates strong opportunities for manufacturers who can effectively differentiate their offerings through strategic customization approaches. Different research organizations project market values ranging from conservative estimates to more optimistic scenarios, highlighting the dynamic nature of this sector.
Market Overview and Growth Dynamics
The global commercial dishwasher market exhibits strong fundamentals driven by expanding foodservice operations, heightened hygiene standards, and technological advancement integration. Market analysts report varying projections, with compound annual growth rates ranging from 3.1% to 8.33% depending on regional factors and segment focus.
Key market drivers include the growing restaurant industry, increased emphasis on energy efficiency, and the rising adoption of IoT-enabled equipment for operational optimization. The market serves diverse applications from small restaurants processing 20-60 racks per hour to high-volume central kitchens requiring 200-400 racks per hour capacity.
Three-Tier Customization Framework
Tier 1: Parameter Selection
Parameter Selection represents the most accessible customization level, focusing on component upgrades within existing machine architectures. This tier primarily involves selecting enhanced pump power configurations, upgrading spray arm materials from standard plastic to stainless steel variants, and integrating internal pressure boosters for improved performance consistency.
The practical applications of parameter selection are most evident in chain restaurant environments where standardized equipment must adapt to varying water pressure conditions and volume requirements. Operators frequently encounter situations where standard pump configurations prove insufficient during peak service periods, necessitating higher-capacity pumps that can maintain consistent wash quality under increased load conditions.
Material upgrades, particularly spray arm components, demonstrate measurable performance improvements in high-volume applications. Stainless steel spray arms exhibit superior durability compared to plastic alternatives, reducing replacement frequency and maintenance downtime. Internal pressure boosters address common operational challenges in locations with inconsistent municipal water pressure, ensuring reliable rinse cycle performance regardless of external supply variations.
Tier 2: Module Modification
Module Modification represents an intermediate customization level that introduces significant functional enhancements while maintaining core machine architecture. This tier encompasses heat recovery systems, heat pump integration, IoT gateway installation, and aesthetic modifications including custom shell colors and protective films.
Heat recovery systems demonstrate substantial operational benefits in commercial applications, particularly in energy-conscious establishments. These systems capture steam generated during wash cycles, redirecting thermal energy to preheat incoming water supplies. Practical implementation shows energy consumption reductions of 5-8 kilowatts per operational hour, translating to meaningful cost savings in high-volume environments.
IoT gateway integration enables real-time monitoring and predictive maintenance capabilities that prove invaluable in multi-location operations. Restaurant chains utilize these systems to monitor machine performance across multiple sites, identifying maintenance requirements before equipment failures occur. The technology facilitates remote diagnostics, reducing service call requirements and minimizing operational disruptions.
Aesthetic modifications serve important branding and environmental integration purposes, particularly in open kitchen concepts and demonstration environments. Custom shell colors and protective films allow equipment to blend seamlessly with designed spaces while maintaining commercial functionality.
Tier 3: OEM/ODM Solutions
OEM/ODM development represents comprehensive customization involving complete machine redesign, custom sizing, and washing system engineering modifications. This tier requires substantial non-recurring engineering investments and extended development timelines but delivers entirely customized solutions for specialized applications.
Central kitchen operations frequently require OEM solutions due to unique spatial constraints and extreme volume requirements. Standard commercial dishwashers prove inadequate for facilities processing 300-400 racks per hour while maintaining strict food safety protocols. Custom sizing allows optimal space utilization in purpose-built facilities where every square foot impacts operational efficiency.
Hospital Sterile Processing Departments demand specialized washing systems that exceed standard commercial specifications. These applications require precise temperature control, specialized rack configurations for medical instruments, and compliance with healthcare regulatory standards that standard equipment cannot address.
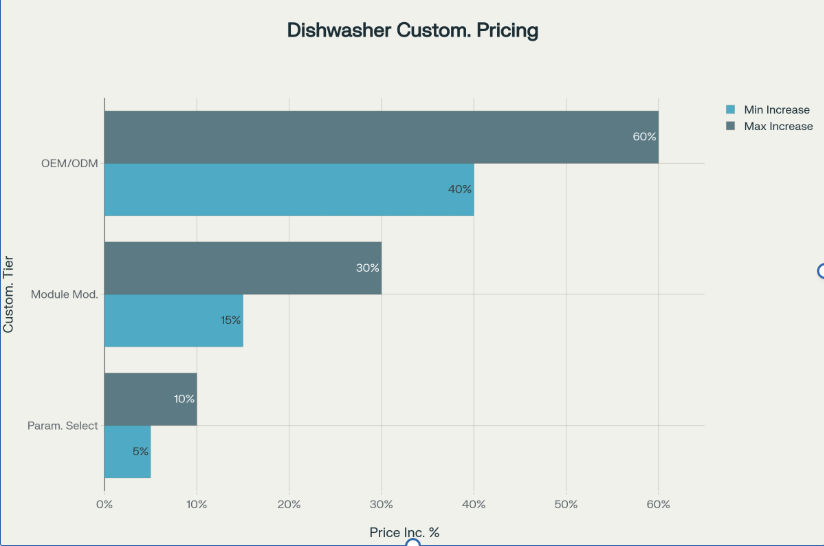
Commercial dishwasher customization pricing tiers showing progressive cost increases from parameter selection to full OEM/ODM development
The cost structure for OEM/ODM solutions reflects the comprehensive engineering investment required, including tooling development, prototype testing, and certification processes. Non-recurring engineering costs typically range from substantial five-figure to six-figure investments depending on complexity levels.
Application-Specific Requirements Analysis
Different commercial applications demonstrate distinct throughput requirements and customization preferences based on operational characteristics and regulatory compliance needs.
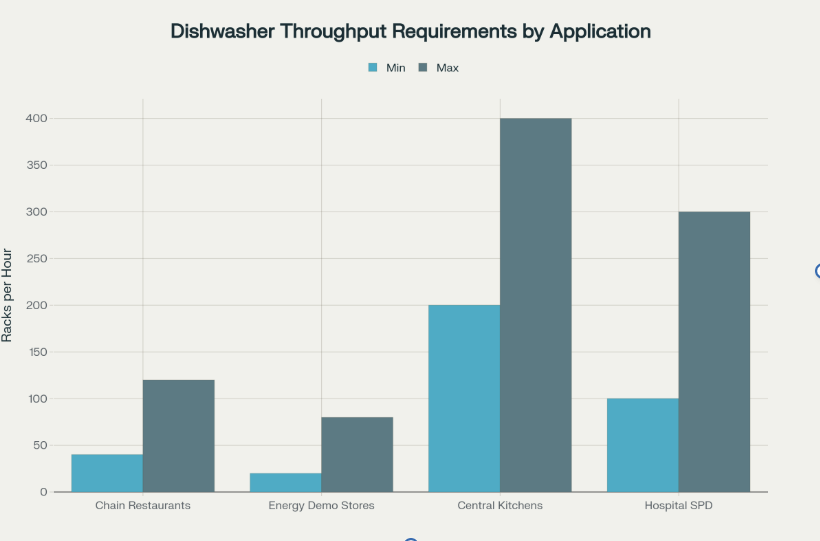
Comparison of dishwasher throughput requirements across different commercial applications
Chain restaurants typically operate within the 60-200 racks per hour range, making Parameter Selection customization most appropriate for addressing specific operational challenges without excessive cost burden. These establishments benefit from pump power upgrades and spray arm material improvements while maintaining standardized maintenance procedures across multiple locations.
Energy demonstration stores present unique requirements where equipment serves dual purposes of functional operation and educational display. Module Modification tier customization proves ideal for these applications, incorporating IoT monitoring capabilities and energy recovery systems that demonstrate sustainability technologies while maintaining operational efficiency.
Central kitchens and hospital SPD facilities represent the highest-demand applications requiring OEM/ODM solutions. These environments demand custom-engineered systems capable of sustained high-volume operation while meeting specialized regulatory requirements that standard equipment cannot address.
Cost-Benefit Analysis and Implementation Considerations
The three-tier customization framework provides structured approaches to balancing customization benefits against implementation costs and timelines. Parameter Selection offers the most favorable cost-to-benefit ratio for standard commercial applications, delivering meaningful performance improvements with minimal cost increase and short implementation periods.
Module Modification presents intermediate value propositions that prove particularly attractive for sustainability-focused operations and multi-location businesses requiring centralized monitoring capabilities. The 15-30% cost premium typically recovers through operational efficiencies within 18-24 months in high-volume applications.
OEM/ODM solutions require careful financial analysis due to substantial upfront investments and extended development timelines. However, these solutions prove essential for specialized applications where standard equipment cannot meet operational requirements or regulatory compliance standards.
Implementation timeline considerations significantly impact customization tier selection. Parameter Selection modifications typically integrate seamlessly into regular equipment replacement cycles, while Module Modifications require coordination with installation planning. OEM/ODM solutions necessitate extended planning periods that must align with facility development or major renovation projects.
Strategic Recommendations
Manufacturers should develop clear customization tier positioning that aligns customer requirements with appropriate solutions while maintaining profitable operations. Parameter Selection tiers provide excellent entry points for building customer relationships and demonstrating value-added capabilities.
Module Modification offerings present opportunities for differentiation in increasingly competitive markets while addressing growing demands for sustainability and operational monitoring capabilities. These solutions particularly appeal to corporate customers with multiple locations and environmental responsibility commitments.
OEM/ODM capabilities serve as premium positioning tools that establish manufacturers as full-solution providers for specialized applications. While these projects require significant resource commitments, they generate substantial margins and create competitive barriers through specialized expertise development.
The commercial dishwasher customization landscape continues evolving as operators seek increasingly specific solutions for diverse applications. Successful manufacturers will balance standardization economies with customization capabilities that address genuine operational requirements across the three-tier framework structure.