I have witnessed the evolution of dishwasher technology from basic mechanical systems to sophisticated, energy-efficient appliances incorporating IoT connectivity and advanced materials science. This report provides an in-depth analysis of modern dishwasher construction methodologies and the complex global component market ecosystem that supports this industry.
Executive Summary
The global dishwasher parts and accessories market represents a sophisticated engineering ecosystem valued at approximately $2.1 billion in 2025, with projected growth to $3.1 billion by 2030. Modern dishwashers integrate over ten critical subsystems, each requiring precise engineering specifications and adherence to multiple international standards. The component cost structure reveals materials as the dominant expense at 45% of manufacturing costs, with the stainless steel tub representing the single most expensive component at approximately $120 per unit.
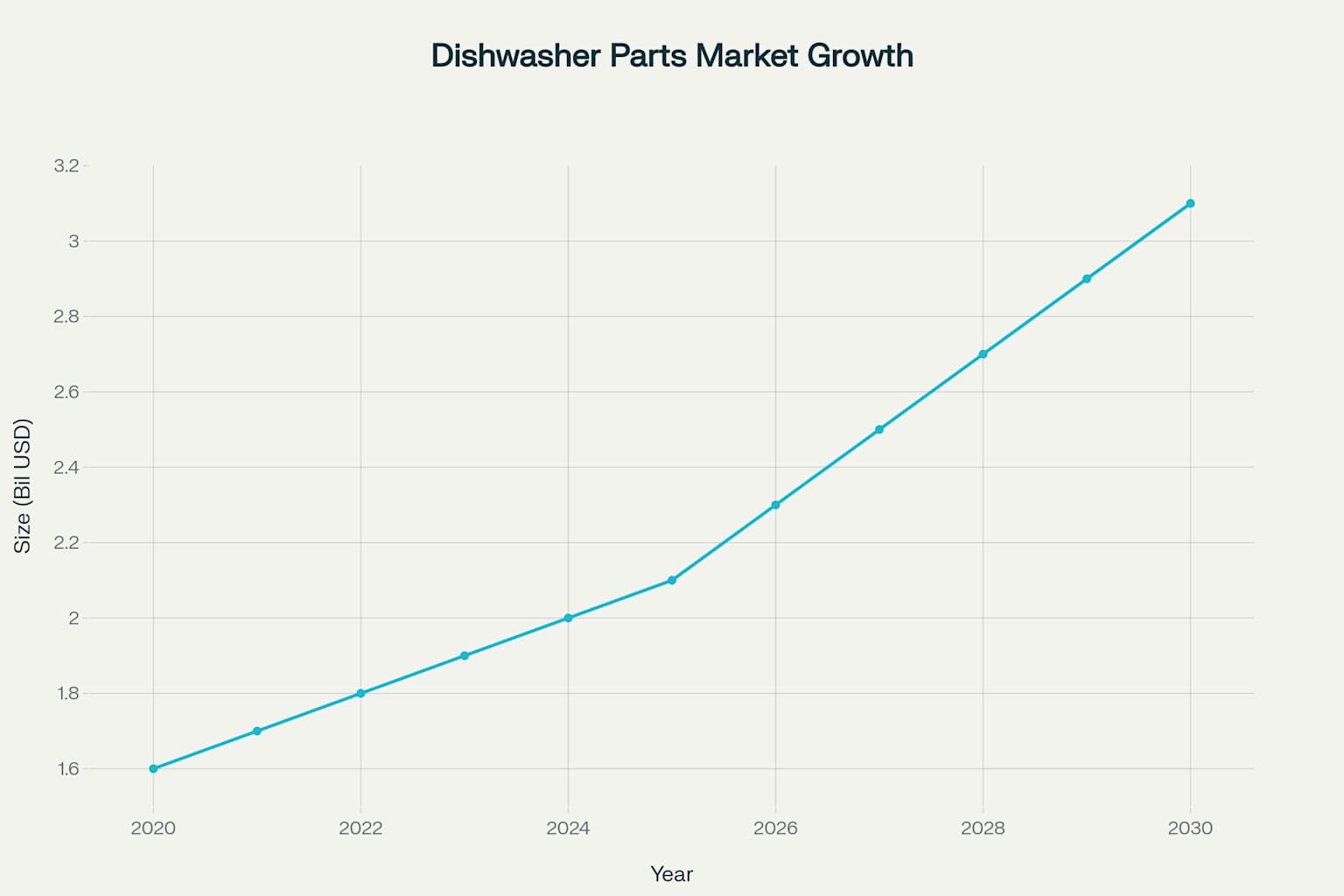
Market growth projection showing dishwasher parts market expanding from $1.6B to $3.1B with corresponding unit sales growth
Fundamental Dishwasher Architecture and Construction
Core Structural Components
From an engineering perspective, dishwasher construction begins with the main tub assembly, which serves as the primary containment vessel and must withstand temperatures up to 82°C while maintaining structural integrity under repeated thermal cycling. The tub construction typically employs either 304-grade stainless steel for premium applications or 430-grade steel for cost-sensitive designs, with the top and bottom sections often utilizing the higher-grade material for enhanced corrosion resistance.
The door assembly represents the second most complex structural component, integrating multiple subsystems including the detergent dispenser, control panel interface, and critical sealing mechanisms. In my experience with door design, the challenge lies in balancing structural rigidity with weight constraints while ensuring perfect alignment with the tub opening across thousands of operational cycles.
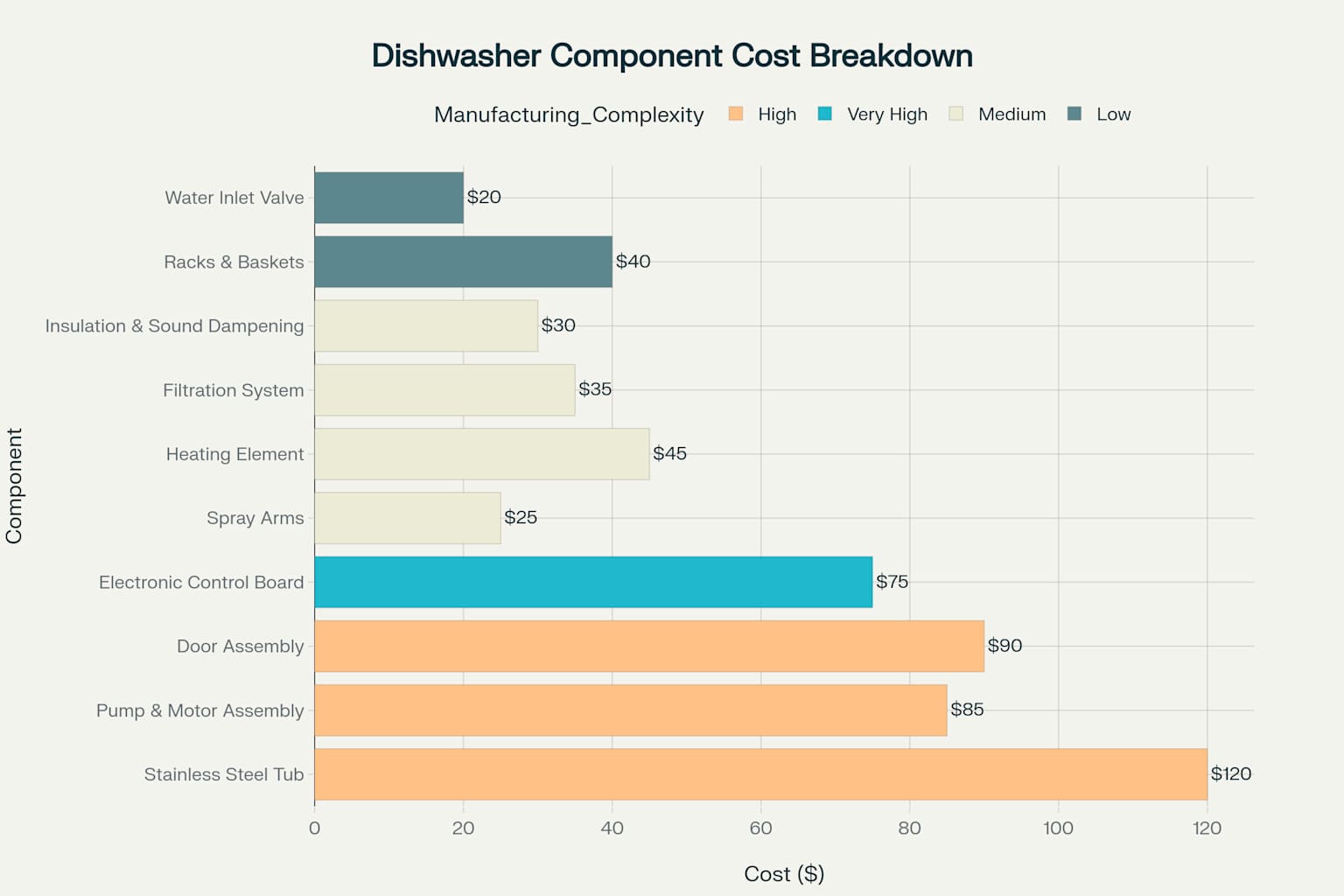
Breakdown of individual dishwasher component costs showing the stainless steel tub as the most expensive component at $120
Hydraulic and Thermal Systems
The pump and motor assembly forms the heart of the dishwasher’s hydraulic system, typically generating flow rates between 20-70 liters per minute at operating pressures of 3.0 bar minimum. Modern designs employ either reversible pumps for directional control or direct-drive systems with solenoid-controlled valving, with motor power ratings ranging from 0.37 to 0.75 kW depending on capacity requirements.
Spray arm technology has evolved significantly in recent years, with advanced designs incorporating self-cleaning nozzles and optimized hydraulic geometries to ensure uniform water distribution. The spray arms must maintain consistent performance across varying water hardness conditions while resisting limescale buildup, requiring careful material selection and nozzle sizing.
The heating element system operates at power levels between 1.8-2.4 kW and must achieve rapid thermal response while maintaining energy efficiency compliance with Energy Star standards requiring ≤240 kWh annual consumption.
Electronic Control Architecture
Modern dishwasher control systems represent highly sophisticated embedded computing platforms managing multiple sensors, actuators, and user interface elements. The electronic control board serves as the central processing unit, coordinating water temperature regulation, cycle timing, pump operation, and safety interlocks. These systems must operate reliably in high-humidity, high-temperature environments while maintaining electromagnetic compatibility standards.
From my R&D experience, the control board design requires careful consideration of component placement, thermal management, and moisture protection through conformal coating applications. Microcontrollers with integrated analog-to-digital converters process inputs from temperature sensors, water level detectors, and turbidity sensors to optimize cleaning performance.
Manufacturing Processes and Quality Control
Assembly Line Integration
Dishwasher manufacturing employs highly automated assembly processes utilizing robotic arms and conveyor systems to ensure precision and consistency. The manufacturing sequence begins with tub fabrication, where single sheets of stainless steel undergo stamping, forming, and welding operations to create the primary containment vessel.
Component integration follows a carefully orchestrated sequence, beginning with the installation of the pump/motor assembly, followed by spray arms, heating elements, and filtration systems. Each assembly station incorporates quality checkpoints including leak testing, electrical continuity verification, and dimensional inspections.
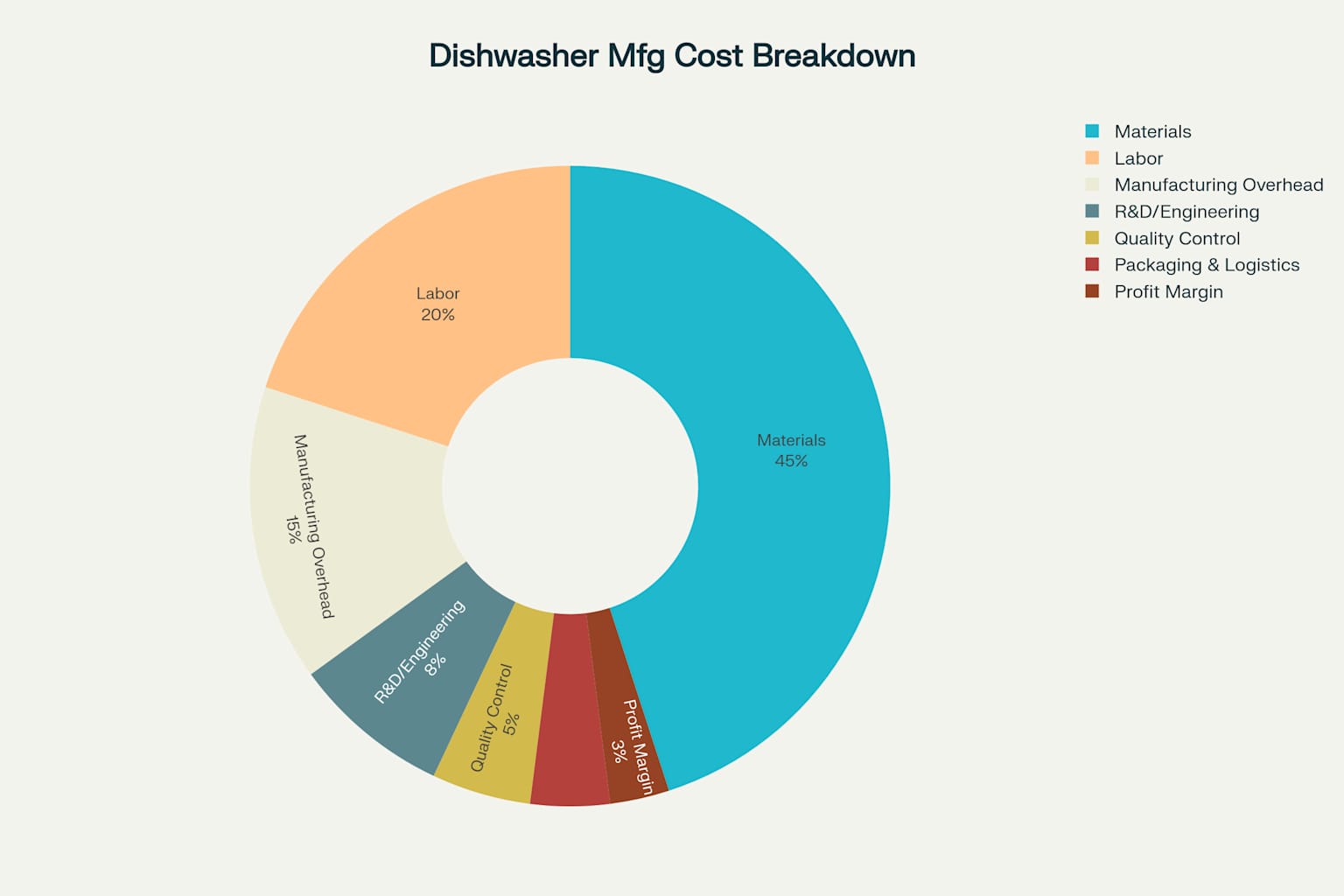
Manufacturing cost distribution showing materials as the largest component at 45% of total costs
Testing and Validation Protocols
Quality assurance in dishwasher manufacturing requires adherence to multiple international standards including NSF/ANSI 184 for residential units and NSF/ANSI 3 for commercial applications. These standards mandate bacterial reduction effectiveness of 99.999% (5-log reduction) and specific temperature requirements during rinse cycles.
Performance testing protocols simulate real-world operating conditions including water hardness variations, soil load testing, and energy consumption validation. Commercial units must demonstrate compliance with specific flow rates and temperature maintenance under continuous operation scenarios.
During my tenure in R&D, we implemented comprehensive thermal cycling tests exposing units to 5,000+ wash cycles to validate component durability and identify potential failure modes . These accelerated aging protocols help predict field performance and optimize component selection .
Global Component Market Analysis
Regional Manufacturing Distribution
The global dishwasher component supply chain exhibits distinct regional specializations, with Germany leading at 22% market share primarily through premium component manufacturing by Bosch, Siemens, and Miele. China represents 18% of global production, focusing on cost-effective manufacturing through companies like Midea and Haier, while the United States maintains 16% market share through Whirlpool and GE operations.
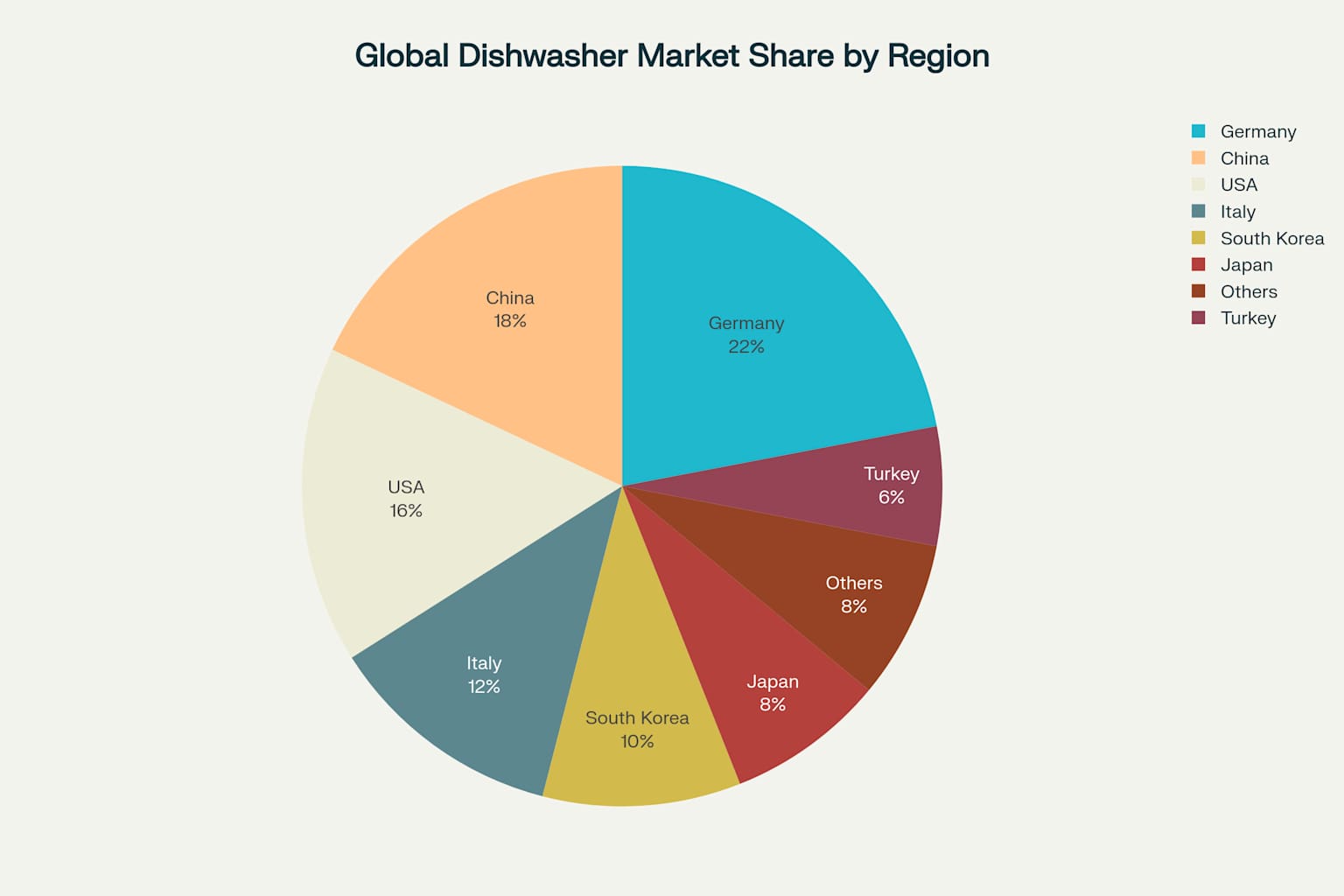
Regional distribution of dishwasher component suppliers with Germany leading at 22% market share
Supply Chain Dynamics and Sourcing Strategies
Component sourcing in the dishwasher industry requires careful balance between cost optimization, quality assurance, and supply chain resilience. Critical components such as pump assemblies and electronic control boards typically source from established suppliers with demonstrated quality systems and long-term supply agreements.
The spray arm and rack systems represent commoditized components with multiple supplier options, allowing for competitive sourcing strategies while maintaining quality standards. However, proprietary designs and brand-specific fitments often limit interchangeability, creating challenges for aftermarket support.
From a procurement perspective, semiconductor shortages have significantly impacted control board availability, necessitating design modifications and alternative component selections. This has driven increased focus on supply chain diversification and strategic inventory management.
Market Growth Projections and Emerging Trends
The dishwasher components market demonstrates robust growth prospects with a projected compound annual growth rate of 4.7% through 2030. Key growth drivers include increased dishwasher adoption in developing markets, replacement part demand from aging installed base, and technological advancement toward smart home integration.
IoT-enabled components represent a rapidly expanding segment, with manufacturers developing connected sensors, diagnostic systems, and predictive maintenance capabilities. These advanced features command premium pricing while creating new market opportunities for component suppliers.
Cost Analysis and Economic Factors
Component Cost Structure Analysis
Detailed cost analysis reveals the stainless steel tub as the highest-cost individual component at approximately $120 per unit, representing 21% of total component costs. The pump and motor assembly follows at $85, with the electronic control board at $75, reflecting the high value-added nature of these engineered subsystems.
Manufacturing cost distribution shows materials comprising 45% of total costs, followed by labor at 20% and manufacturing overhead at 15%. This cost structure emphasizes the importance of material selection and supply chain optimization in achieving competitive pricing.
Total component costs aggregate to approximately $565 per unit, representing 94% of manufacturing costs when including assembly, testing, and overhead expenses. This high component-to-manufacturing cost ratio indicates limited opportunity for cost reduction through process improvements alone, necessitating focus on component design optimization and supply chain efficiency.
Market Positioning and Price Segmentation
The dishwasher market segments into distinct categories based on feature content, performance specifications, and target pricing. Budget segments ($300-500) utilize simplified control systems and standard efficiency ratings, while premium segments ($900-1500+) incorporate advanced features including multiple wash zones, smart connectivity, and ultra-quiet operation below 44 dB.
Commercial applications command significantly higher pricing ($3000-8000+) due to enhanced durability requirements, higher capacity specifications, and specialized sanitization capabilities. These units incorporate heavy-duty pump systems, reinforced construction, and accelerated cycle times to meet foodservice industry demands.
Industry Standards and Regulatory Compliance
Performance and Safety Standards
Dishwasher design must comply with comprehensive performance and safety standards varying by geographic market and application. NSF/ANSI 184 governs residential dishwasher sanitization requirements, mandating bacterial reduction effectiveness and specific rinse temperature thresholds of 150°F.
Energy efficiency standards under Energy Star require annual consumption below 240 kWh and water usage under 3.2 gallons per cycle for standard-sized units. These requirements drive continuous innovation in pump efficiency, thermal management, and cycle optimization.
International standards including IEC 60436 and EN 50242 establish global harmonization frameworks for performance testing and energy labeling. Compliance with these standards requires extensive testing protocols and design validation across multiple operating conditions.
Testing Methodologies and Validation
Professional dishwasher testing employs standardized soil loads, water hardness specifications, and measurement protocols to ensure repeatable results. Cleaning performance evaluation utilizes controlled soiling materials including cherry pie filling and standardized food residues to simulate real-world conditions.
Temperature monitoring during test cycles requires precision instrumentation capable of measuring surface temperatures on dishware to verify sanitization effectiveness. These measurements confirm that rinse water temperatures translate to actual surface heating sufficient for bacterial elimination.
From my laboratory experience, we utilize specialized temperature strips and data logging equipment to validate thermal performance across complete wash cycles. This testing reveals the critical importance of proper water circulation and contact time in achieving sanitization targets.
Future Outlook and Technological Trends
Emerging Technologies and Innovation
The dishwasher industry continues evolving toward increased automation, connectivity, and sustainability. Artificial intelligence integration enables predictive maintenance, optimized cycle selection, and real-time performance monitoring. These systems analyze usage patterns and adjust operating parameters to maximize efficiency while maintaining cleaning effectiveness.
Sustainable materials and manufacturing processes represent growing focus areas, with development of recyclable components, biodegradable filters, and carbon-neutral production methods. Component manufacturers increasingly emphasize environmental impact reduction throughout product lifecycles.
Modular design concepts enable component standardization and improved serviceability, potentially reducing lifecycle costs while enhancing aftermarket support. This approach facilitates design-for-disassembly principles supporting circular economy objectives.
Market Challenges and Opportunities
Component compatibility and standardization remain significant industry challenges, with proprietary designs limiting interchangeability and increasing service complexity. Development of universal components and enhanced compatibility guides represents important opportunities for market expansion.
Supply chain resilience continues as a critical concern following recent disruptions, driving increased focus on regional manufacturing capabilities and supplier diversification strategies. Component manufacturers investing in flexible production capabilities and geographically distributed capacity will likely gain competitive advantages.
The expanding global middle class, particularly in Asia-Pacific markets, creates substantial growth opportunities for dishwasher adoption and component demand. Manufacturers developing cost-effective solutions optimized for diverse water quality conditions and local preferences will capture significant market share in these emerging regions.
Conclusion
Modern dishwasher design represents a sophisticated integration of mechanical, thermal, hydraulic, and electronic systems requiring extensive engineering expertise and global supply chain coordination. The component market exhibits robust growth prospects driven by technological advancement, expanding global adoption, and increasing focus on energy efficiency and sustainability.
Success in this industry demands comprehensive understanding of materials science, manufacturing processes, regulatory requirements, and market dynamics. As dishwasher technology continues evolving toward increased connectivity and environmental responsibility, component suppliers and manufacturers must balance innovation with reliability, cost-effectiveness, and global compatibility.
The engineering challenges ahead include developing intelligent systems capable of autonomous optimization while maintaining the durability and simplicity that consumers expect from this essential household appliance. Through continued investment in research and development, strategic supply chain partnerships, and commitment to quality excellence, the dishwasher industry will continue delivering improved performance and value to global markets.